CUSTOM ECO-FRIENDLY ENGINEERED FLOOR MADE FROM RECLAIMED BLEACHER BOARDS
Here at Pioneer Millworks we have a menu of more than 50 standard products. But we continue to push the envelope and work with clients who come to us with their own unique vision. In fact, nearly half of all the jobs we do each year are custom. We love these partnerships into uncharted waters and all the challenges that they entail. The extra sweat and tears spent in the production of these orders often leaves us feeling especially proud of the end results.
One recent custom order of which passed through nearly every hand in our shop was 8,000 square feet of Eco-Friendly Engineered Floor made from Reclaimed Douglas Fir Bleachers. Destined for a large corporate headquarters in California, here is what was involved:
- Bleachers were sourced from across the nation, from Webster, New York to Portland, Oregon and numerous stops in-between. Because only solid Douglas Fir bleachers could be used for this order, our acquisitions team traveled across the country to find the perfect stock. This was something of a treasure hunt as most bleachers that were installed in the last 50 years are plastic, pine or laminates.
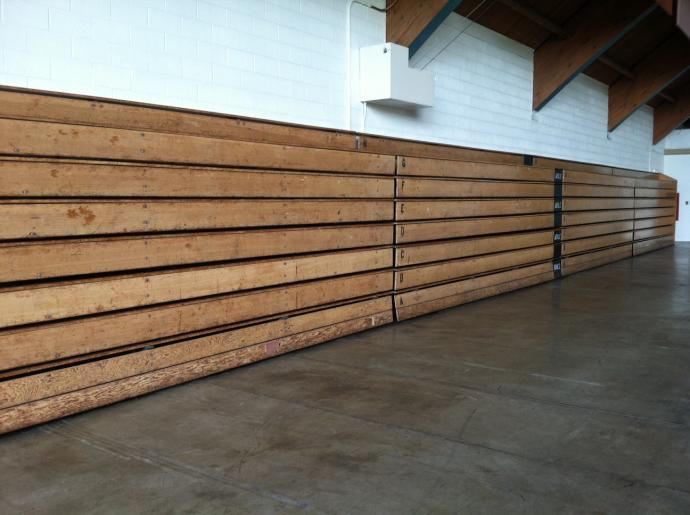
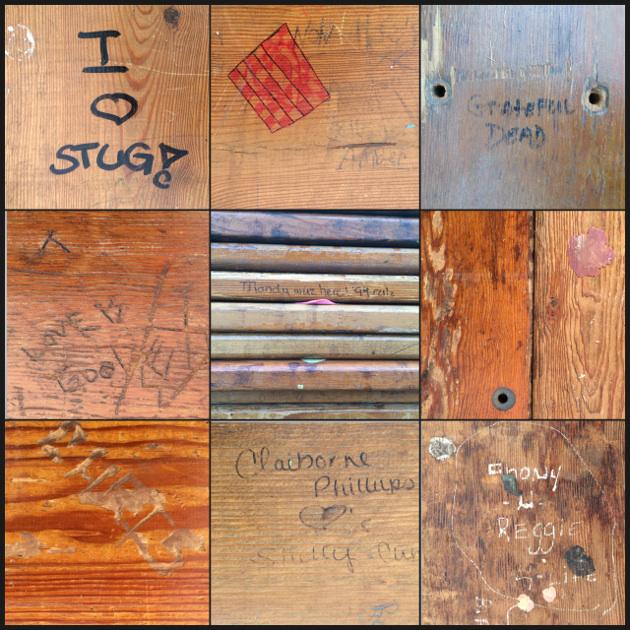
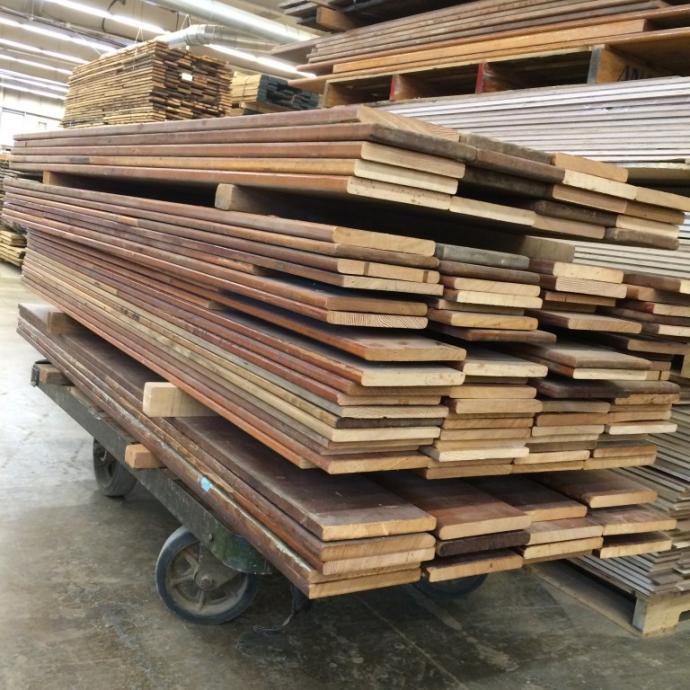
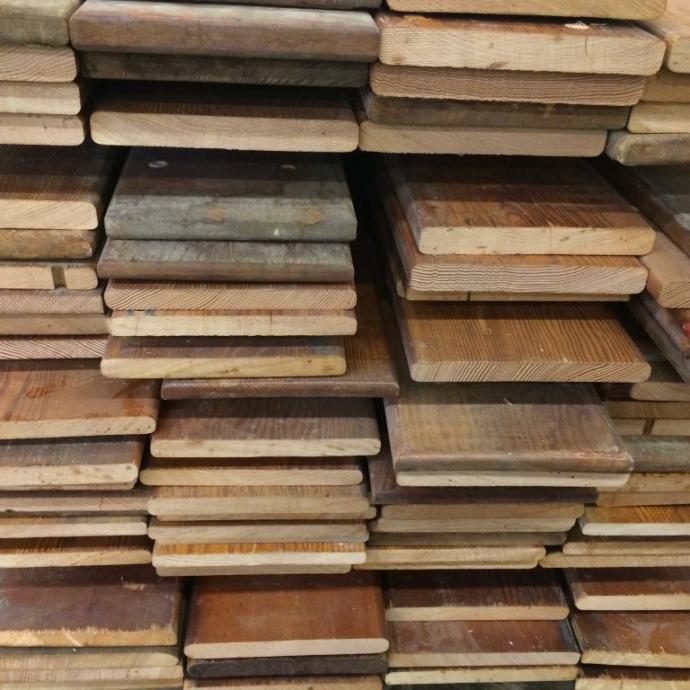
2.After the bleachers were cut to 8′ lengths (the length of the plywood), we fully surfaced each board in our moulder and put them in our kiln for several days. This brought all the wood to a consistent moisture content and killed any nasty fungus that might have resided after decades of sweaty gym shorts leaving their mark (we learned this the hard way).
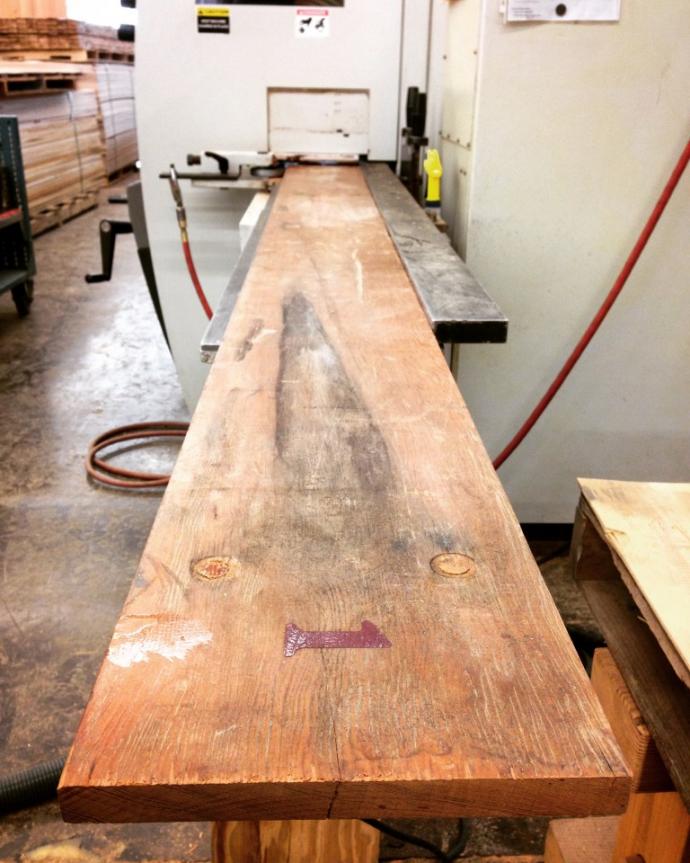
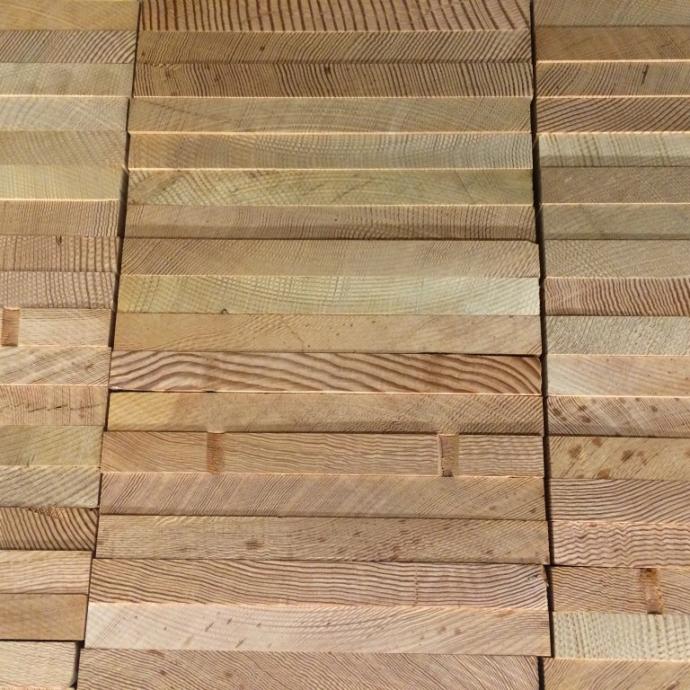
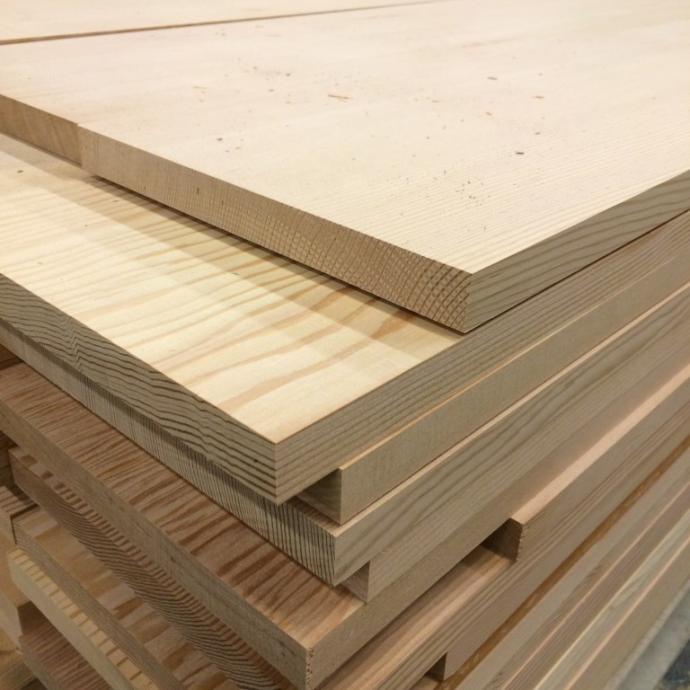
The holes left from the original carriage bolts which once secured the bleachers to a metal frame, are drilled out and filled with custom plugs. Our detail oriented crew did an exceptional job matching the grain of the plugs to the grain of each board.
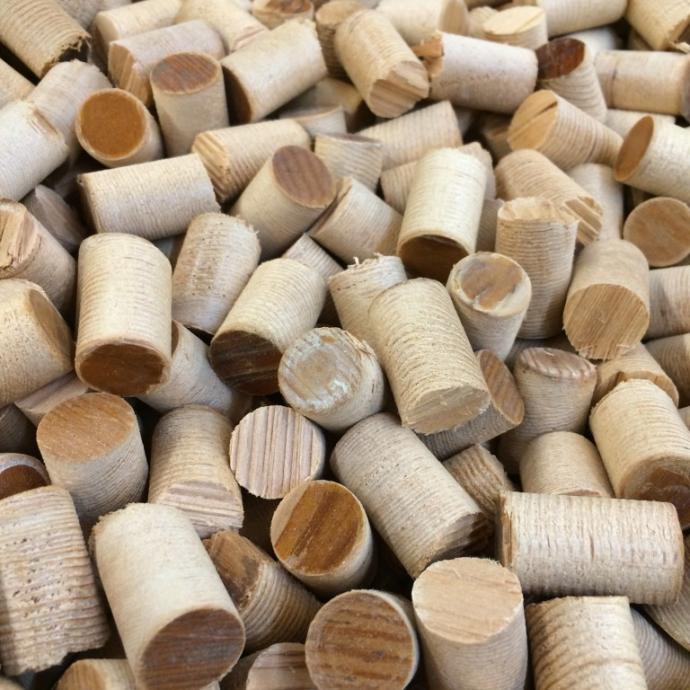
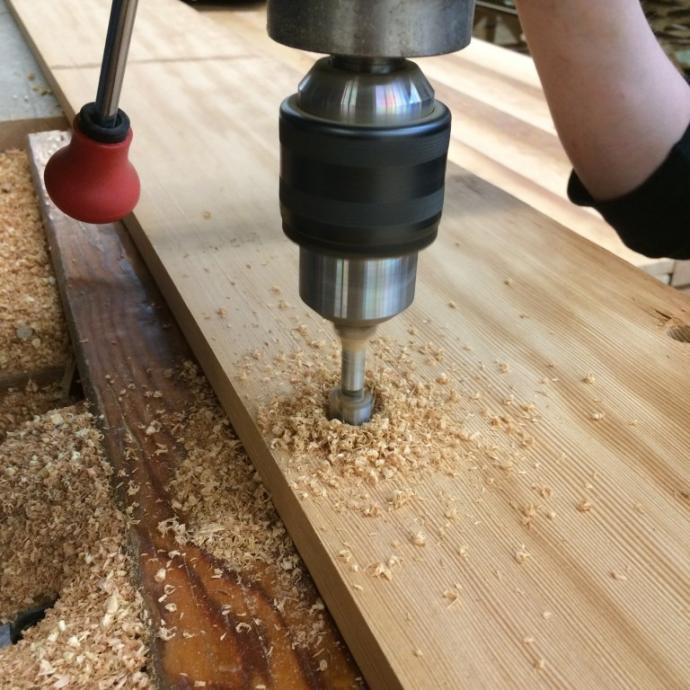
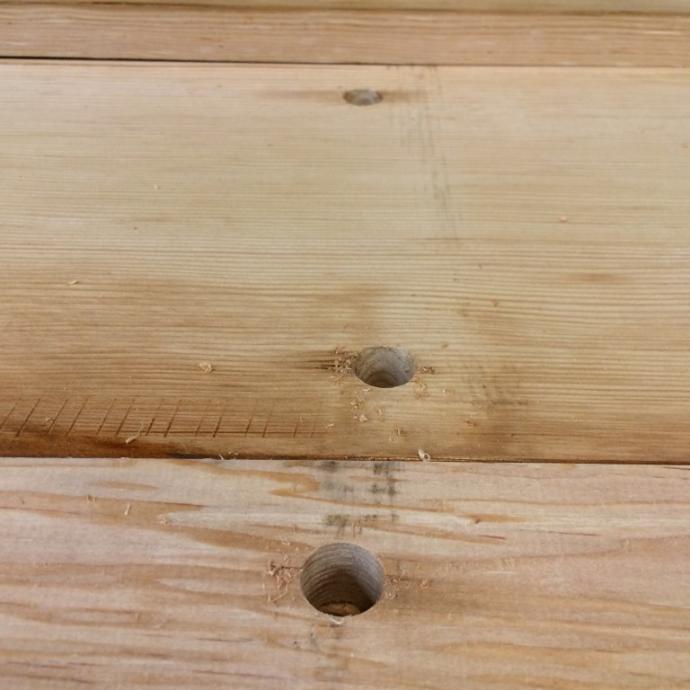
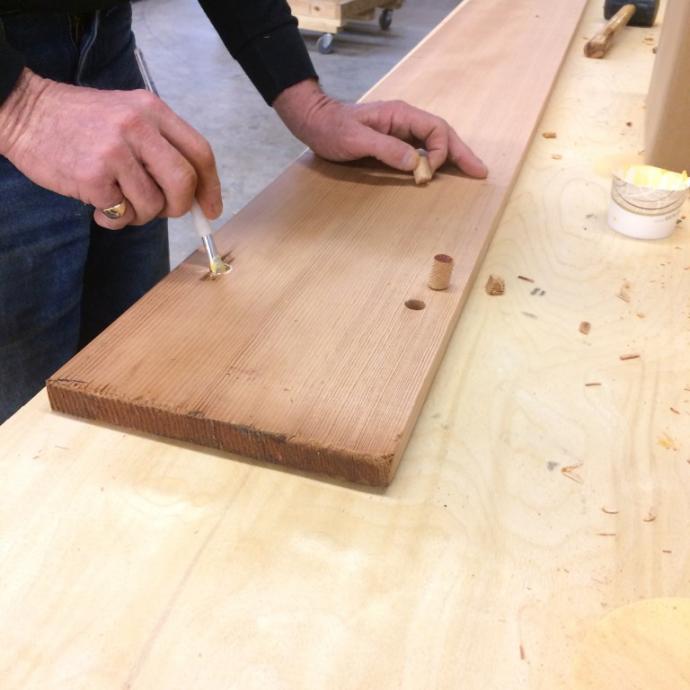
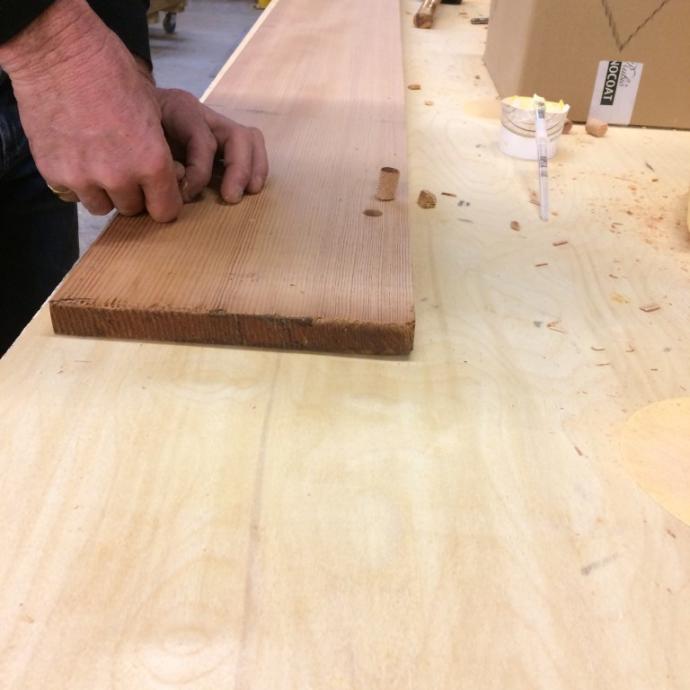
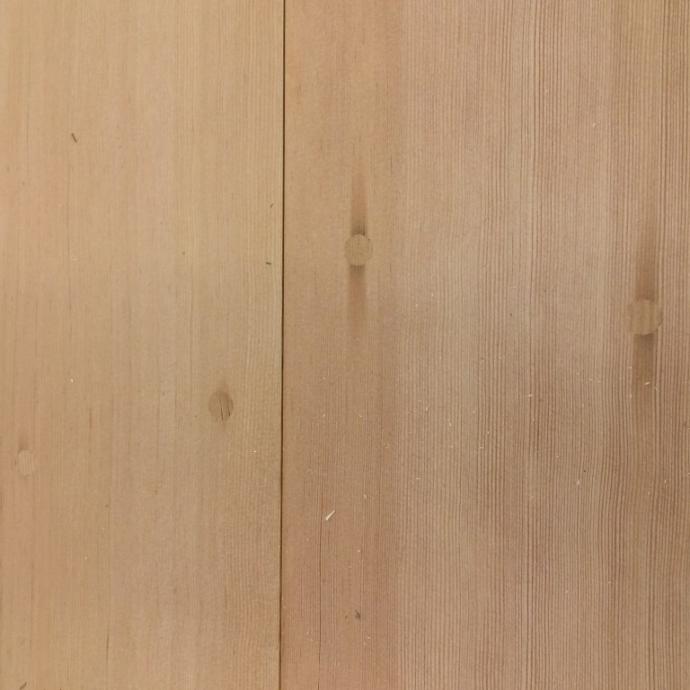
Once plugged, each board was again surfaced in the moulder and then run through our frame saw. Here, a series of blades sawed each board into three thin wear layers.
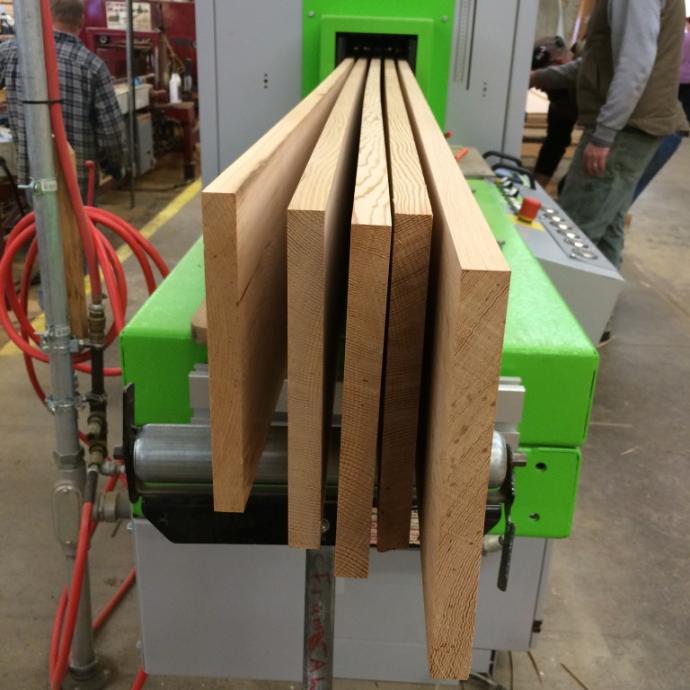
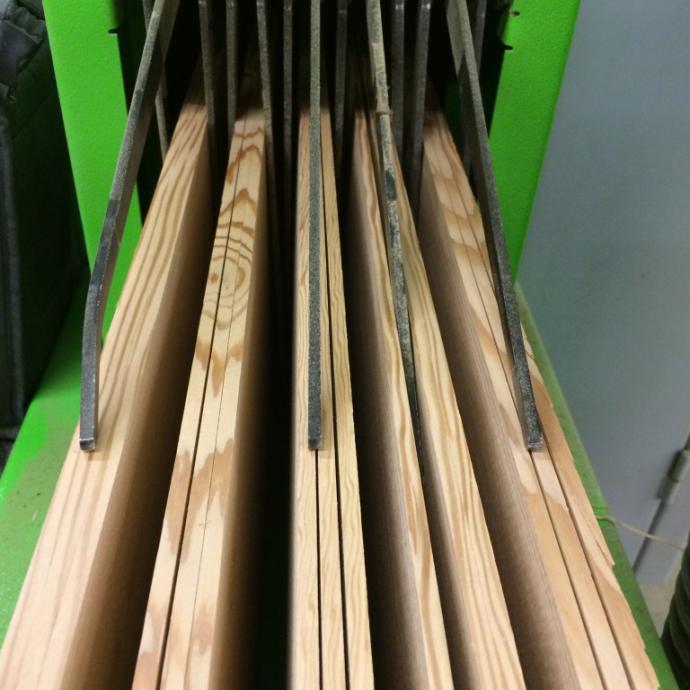
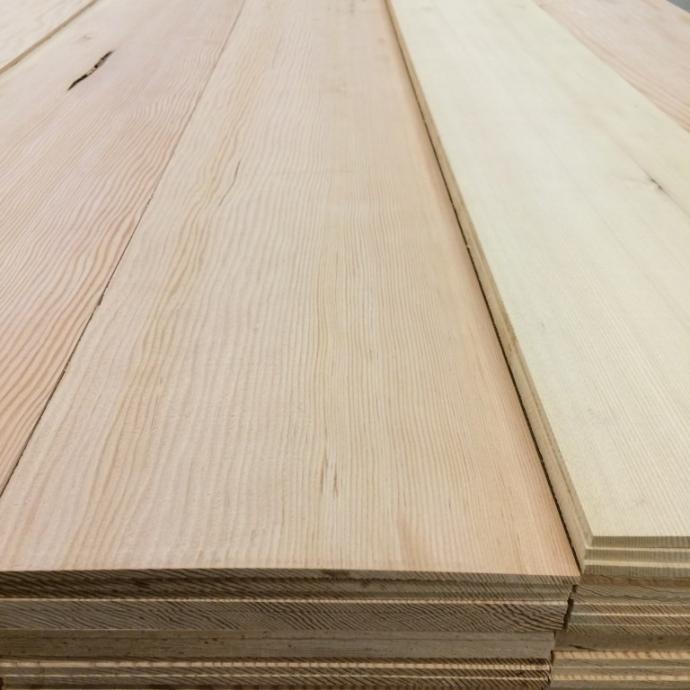
On our glue line, each wear layer was carefully adhered to a FSC® Baltic Birch plywood substrate.
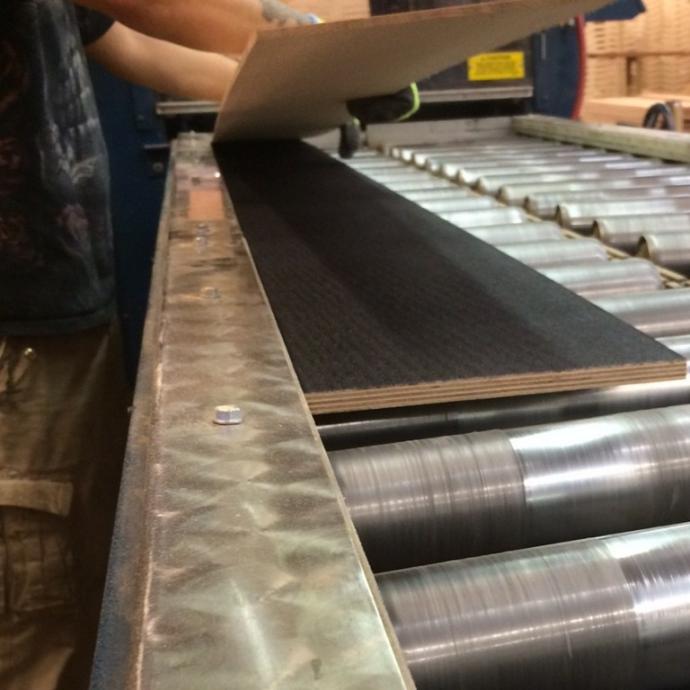
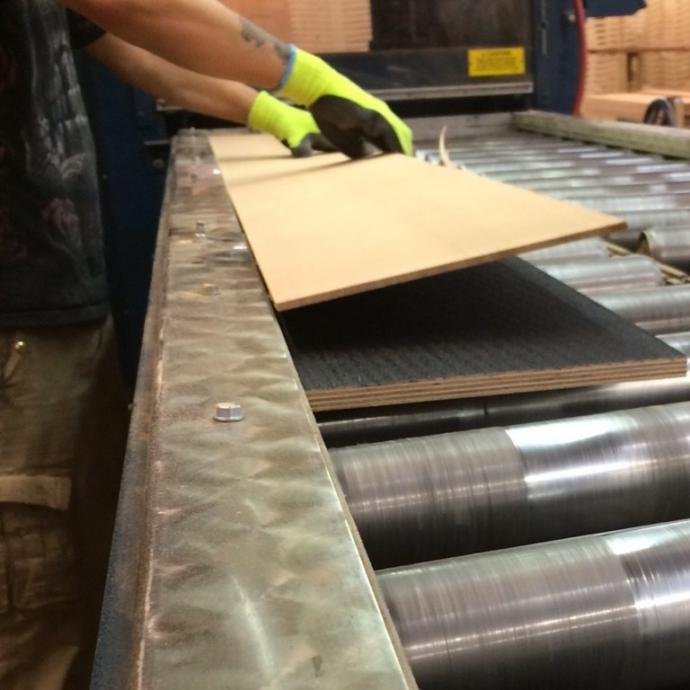
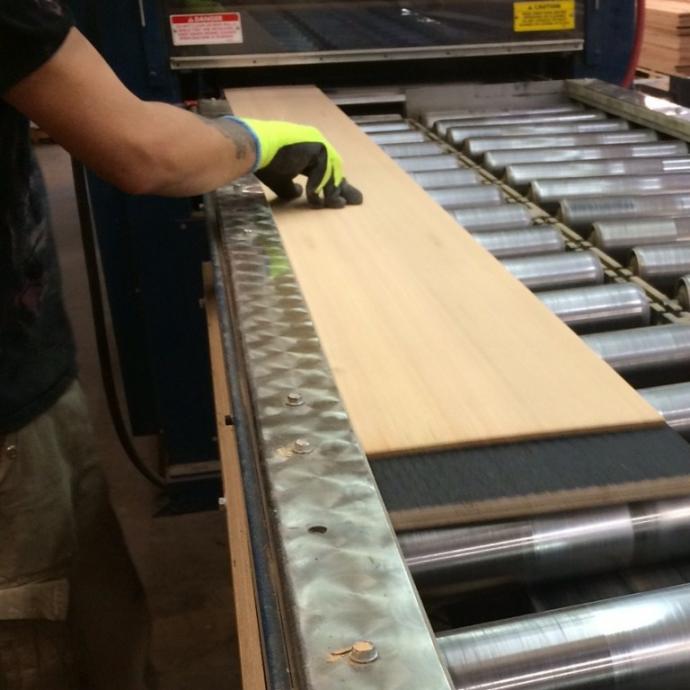
Finally, these glued-up boards were run through the moulder a third and final time where the tongue and groove was milled. After defecting out any remaining irregularities, each board was end-matched and stacked to ship.
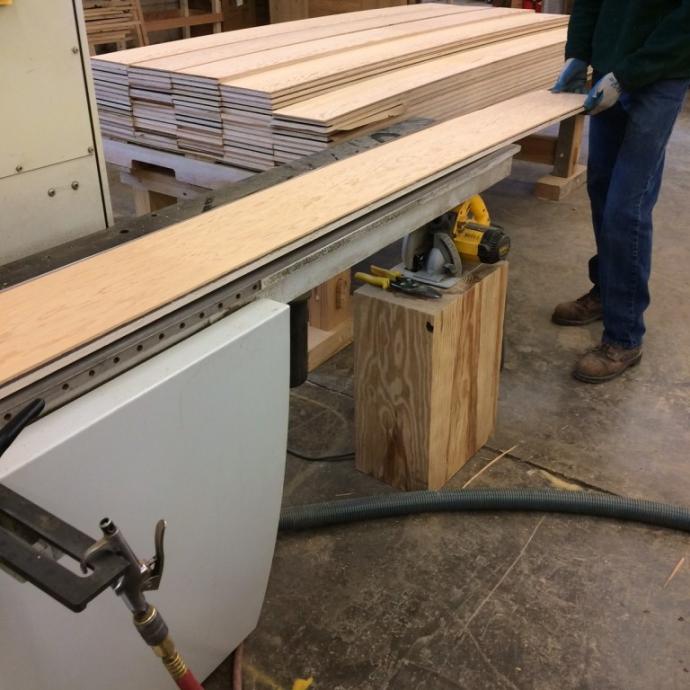
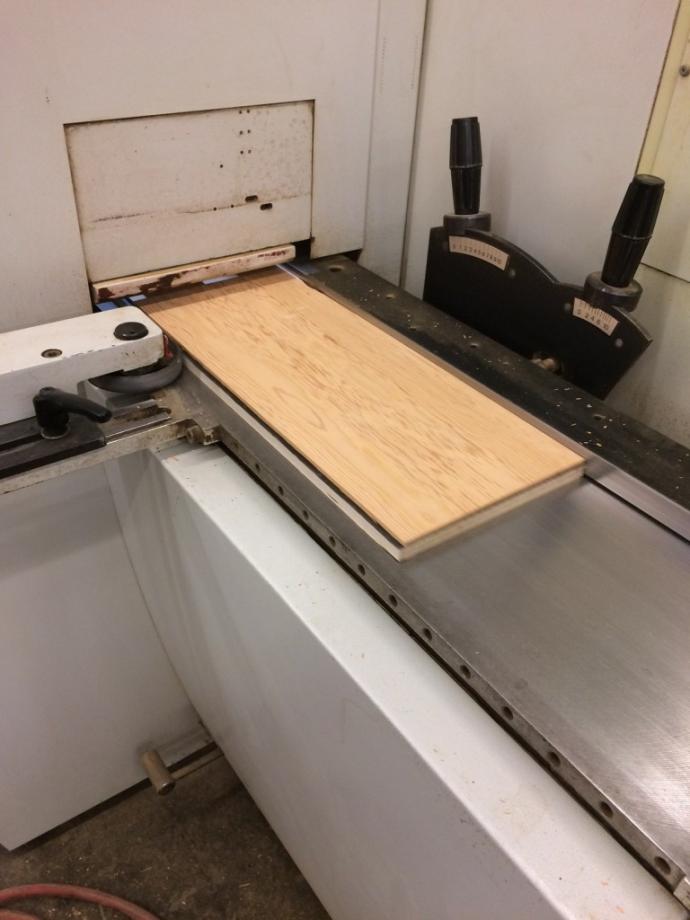
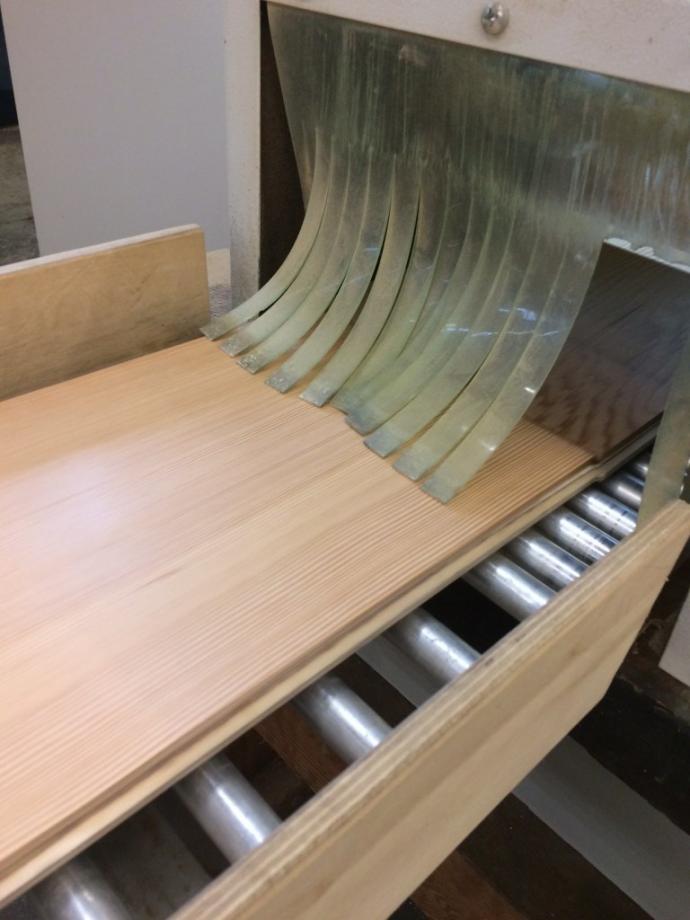
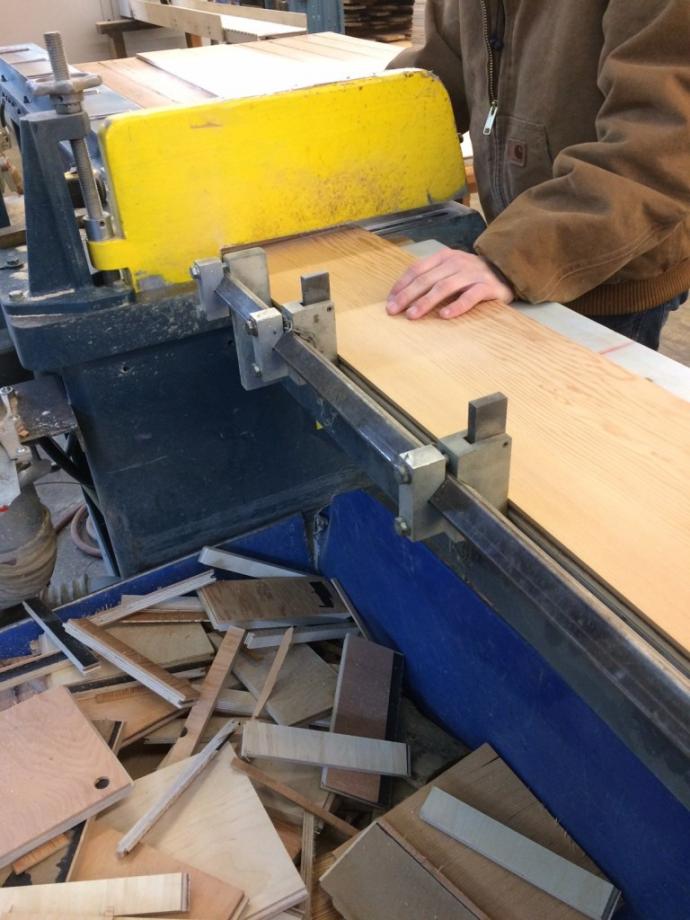
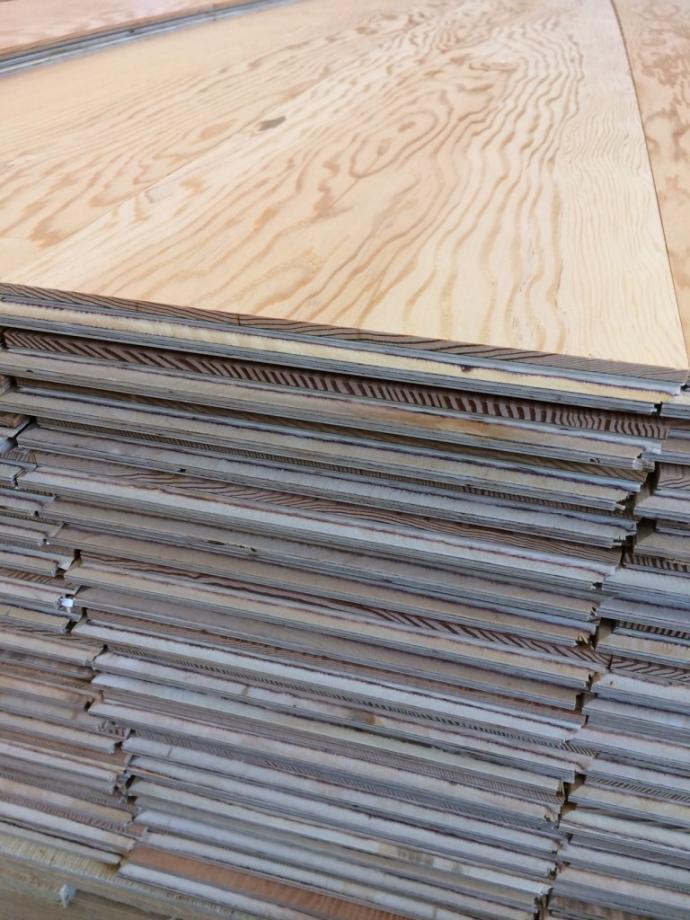
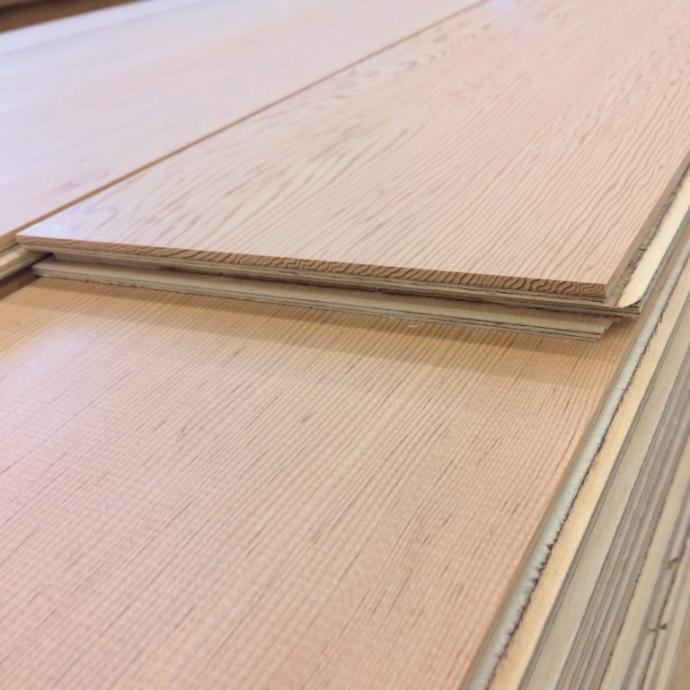
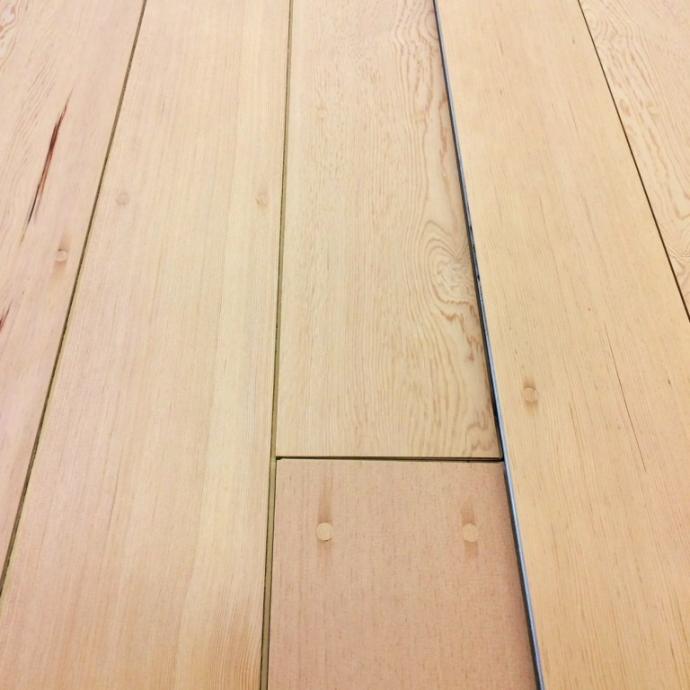
I think that it is safe to say that everyone involved in the project is especially proud of this beautiful one of a kind floor. Keep the custom projects coming!